- Home
- Company
- Products and Technology
- Vibration
Minimize exposure to construction vibration
Active Vibration Reduction (AVR) technology and other practical strategies to help reduce vibration
In the construction industry, workers are unavoidably exposed to some vibration when they drill, chisel, break or grind materials. However, you can calculate, manage and minimize power tool vibration, to help keep construction workers more comfortable and therefore more productive.
As a responsible employer, you naturally want to increase the productivity of your team. So how can you manage the vibration intensity and duration team members are exposed to?
How do you measure power tool vibration on your jobsites?
In some countries it may be necessary for an employer to measure and monitor the vibration employees are exposed to.
As such, employers following European Union-wide Exposure Action Values (EAVs) may need to act when exposure to vibration for an employee reaches 2.5 m/s2 A (8). That means when a construction worker's vibration exposure reaches 2.5 meters per second as an average exposure over an 8-hour day [1].
In addition, the EU sets out Exposure Limit Values (ELVs), for the maximum amount of vibration an individual can be exposed to on a single day being 5 m/s2 A (8).
In Great Britain, the Health and Safety Executive (HSE) publishes a hand-arm vibration exposure calculator [2] to help employers measure and monitor vibration. However, it’s important to realize that a higher m/s2 doesn’t necessarily mean a higher risk. To choose the right tool for the job, you need to consider other factors such as tool performance, corresponding fatigue, and “trigger time” (time spent using vibrating tools).
For these reasons, we recommend you also use the Hilti tool selector – which calculates tool performance – helping you to choose the right tools and reduce exposure time. The selector also gives you information to calculate dust and noise values, which also help to manage health and safety.
So how can you minimize construction vibration, increasing productivity and leading to healthier jobsites? We recommend following the "STOP Principle".
Substitution: eliminate the risks of vibration by using alternatives
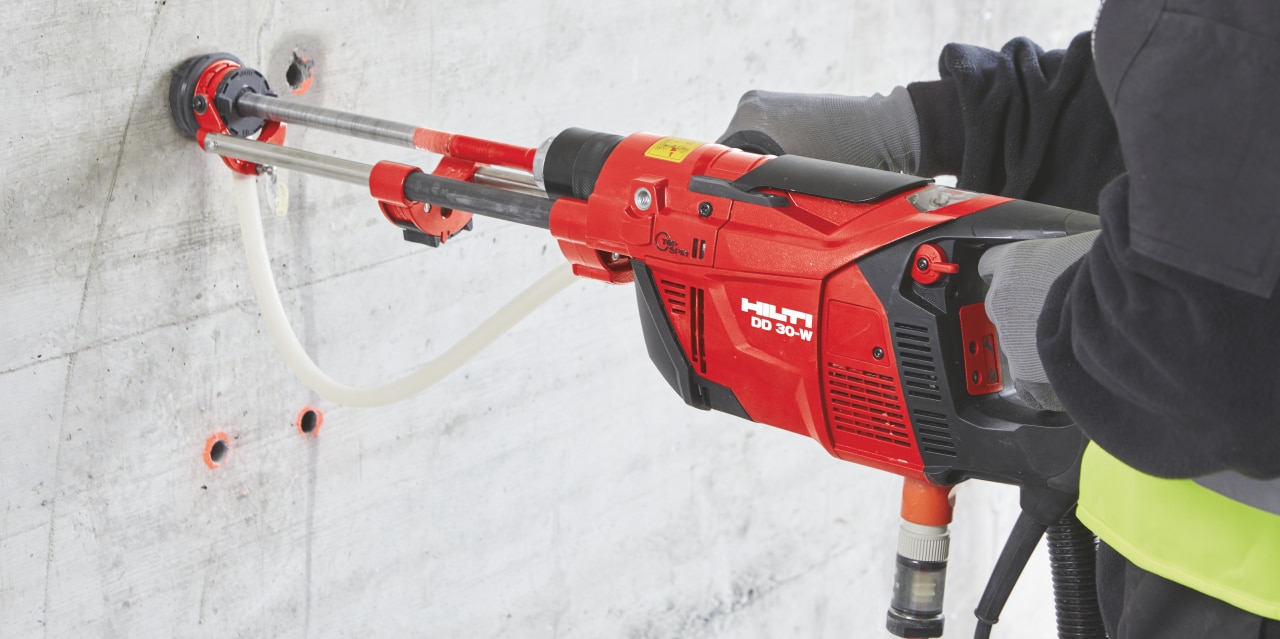
Drilling
Choose low-vibration diamond coring tools, instead of combihammers. Reduce vibration exposure further by using a rig-mounted system.
DD 160 diamond coring tool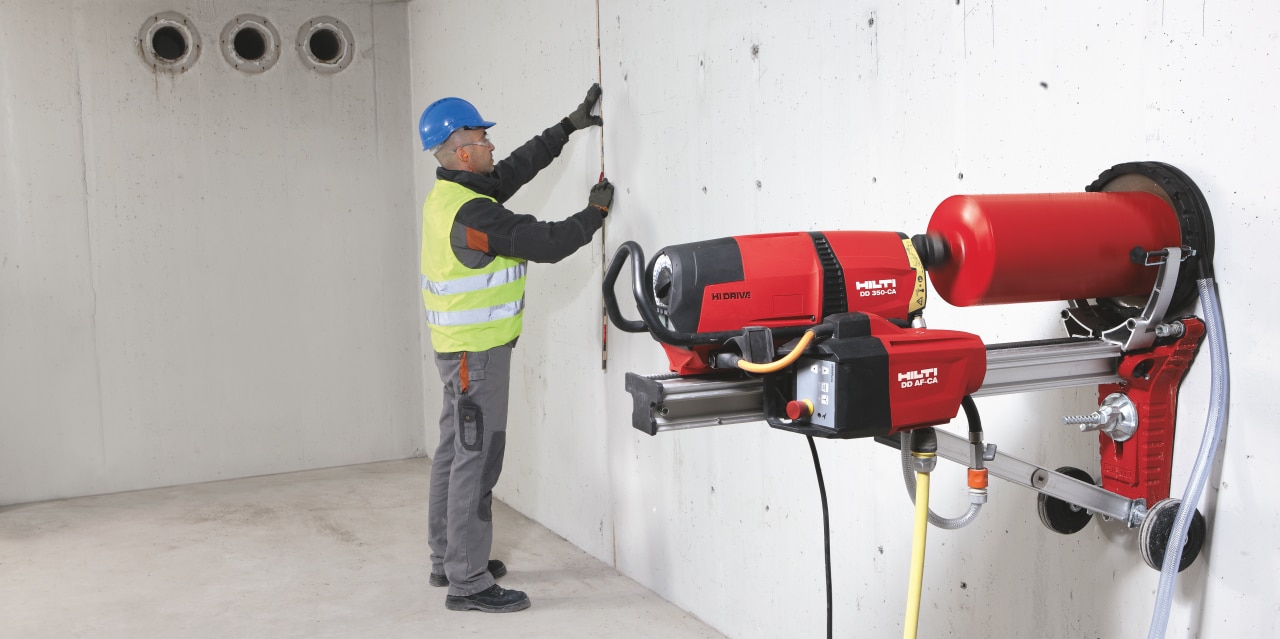
Breaking
Use rig-mounted diamond wall saws and coring tools, instead of hand-held combihammers and breakers. Working with a Cut Assist automatic feed unit makes it a highly efficient and fully automated process.
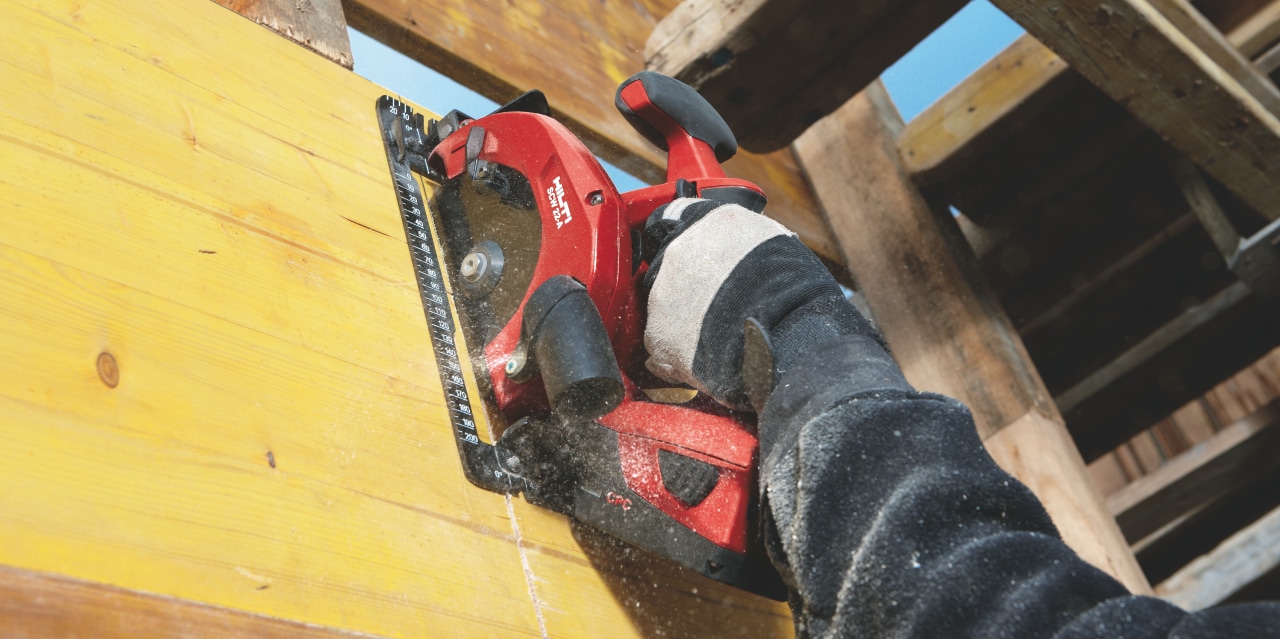
Cutting
Opt for mounted diamond wall saws with Cut Assist, instead of handheld gas saws. When handheld cutting, consider circular saws that have lower vibration values than reciprocating saws.
SCM 22-A cordless circular saw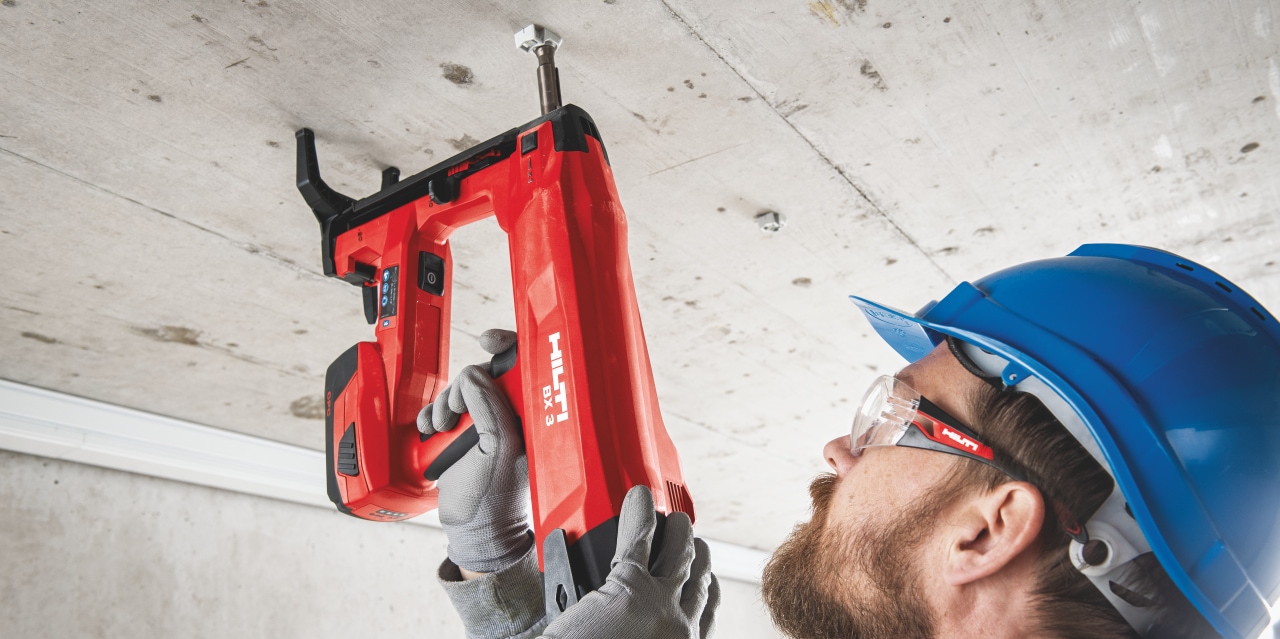
Direct fastening
Switch to low-vibration direct fastening battery-powered nailer– instead of drilling to fasten anchors, screws and studs.
Contact us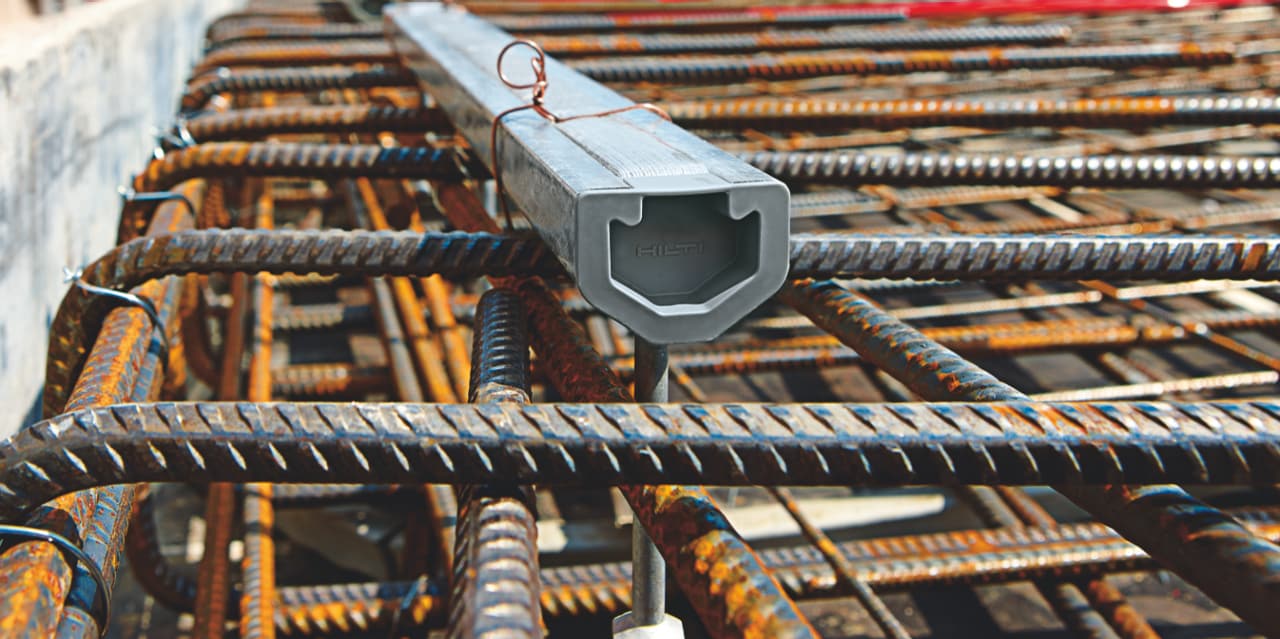
Designing out construction vibration
Place our HAC cast-in anchor channels around the rebar before the concrete is poured, meaning little or no drilling and therefore no vibration.
HAC cast-in anchor channelsTechnical: products to reduce power tool vibration
Through many decades of research and development, Hilti has been minimizing power tool vibration using Active Vibration Reduction (AVR) systems. This technology reduces vibration by up to two-thirds compared to conventional tools, allowing them to be used for longer and more comfortably.
Choosing tools with AVR can significantly reduce vibration without compromising performance, making it easier to keep construction workers comfortable and productive.
Hilti AVR works in a number of ways to reduce power tool vibration to a minimum, including:
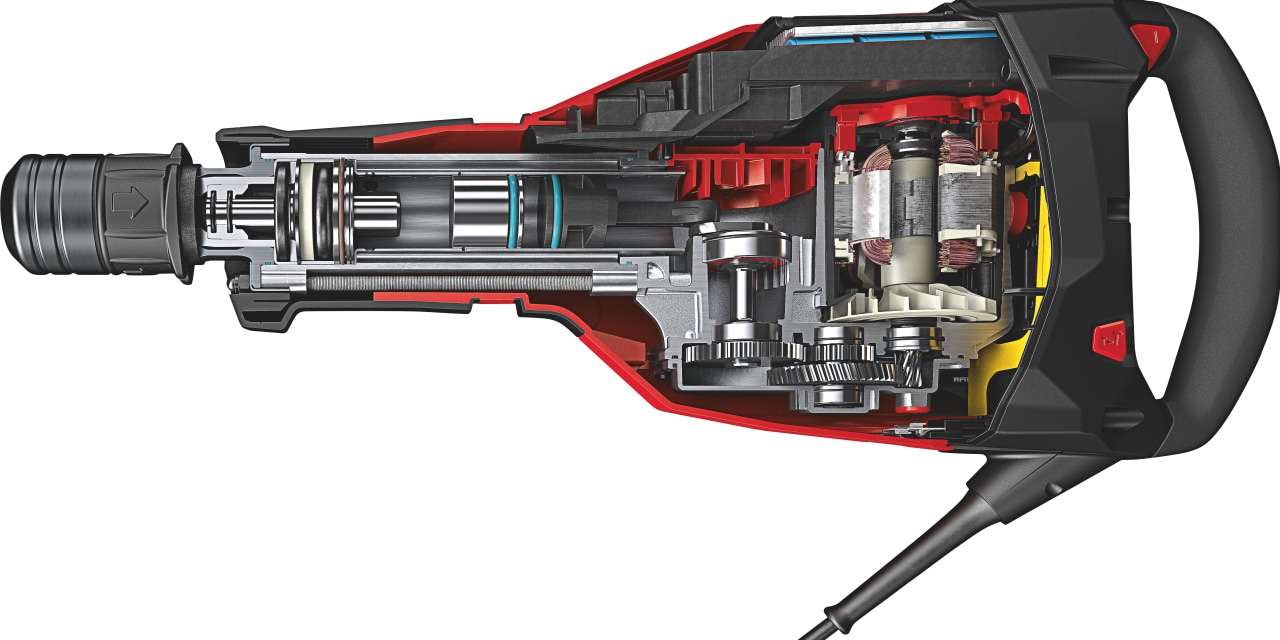
Sub-chassis systems
Feature in tools such as the TE 1000-AVR breaker, where the motor is isolated from the external housing through a suspension system, absorbing vibration that would otherwise pass directly to the user.
Watch video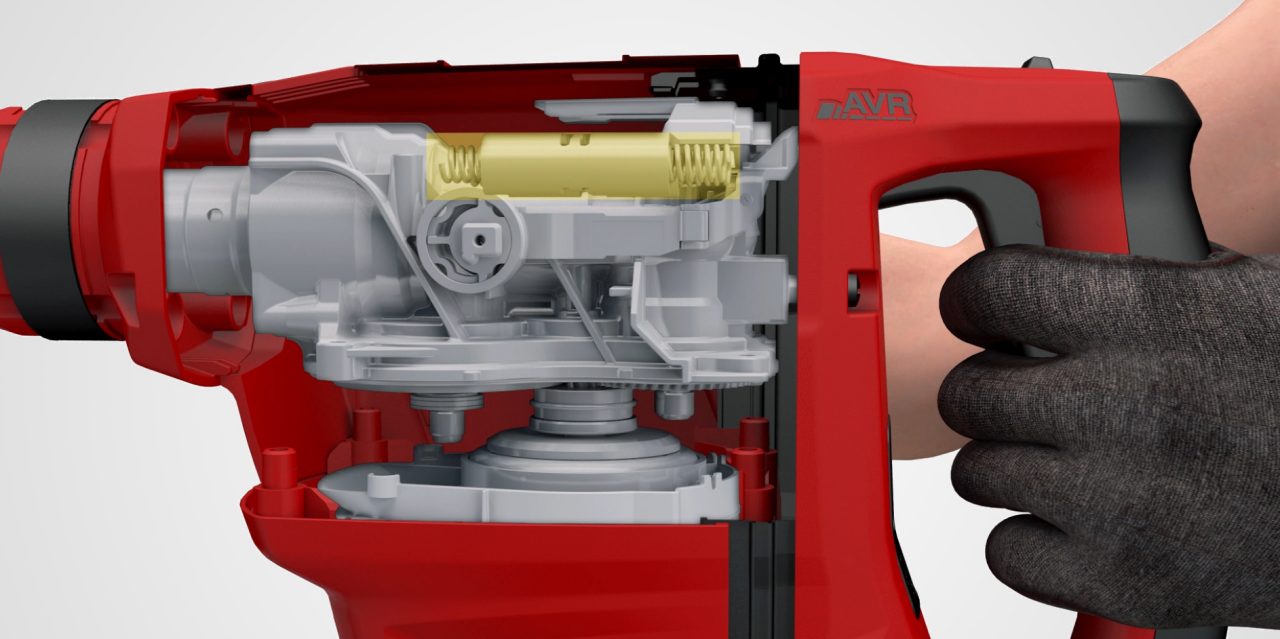
Vibration absorbers
Counterweights oscillate to counteract vibration in combihammers such as the TE 50-AVR, reducing the vibration which reaches the operator's hands.
Watch video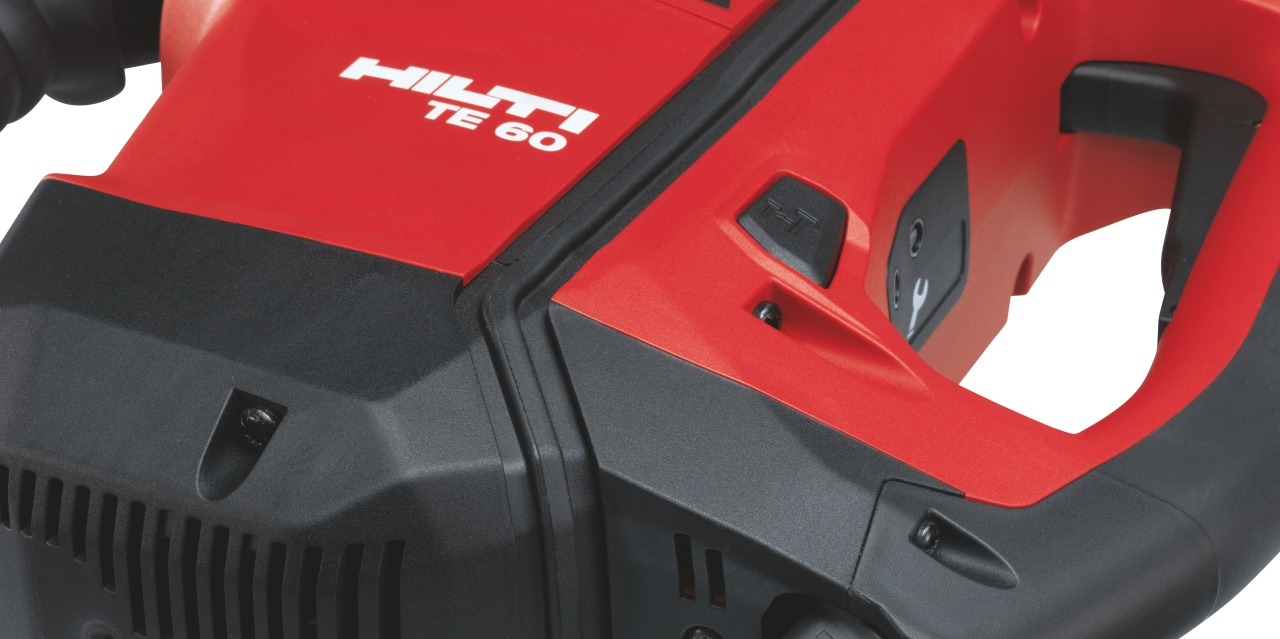
Decoupled handles
Separate the vibrating section of the tool from the user in combihammers such as the TE 60-ATC-AVR, which also features a built-in vibration absorber.
Watch videoOrganizational: measures to reduce vibration exposure
The third stage of the “STOP principle” is to implement organizational measures that cut construction workers’ exposure to vibration to a minimum.
One way you can do this is to create a system of job rotation, making sure that construction workers switch between tasks that involve vibrating tools and others that don’t.
In the same way that you can use quicker, more effective tools to help reduce vibration exposure time, you can also combine them with quality inserts. High performance inserts don’t directly reduce construction vibration but they do help to get the job done faster, reducing trigger time, and therefore overall vibration exposure.
Good examples of consumable upgrades you can make include:
- Drilling: use ultimate TE-CX (SDS plus) hammer drill bits – with 4 carbide cutting edges – to get the job done faster
- Chiseling: opt for self-sharpening TE-SPX chisels which stick less, thanks to their polygon wave design
- Grinding: using SPX diamond cup wheels for faster grinding thanks to the dense concentration of high-quality diamonds, and lower vibration thanks to advanced core balancing technology
Your organization should also make sure team members receive industry training to help minimize vibration exposure. To help you with this, impartial advice and guidance is available from the HSE vibration web pages [3].
Hilti also offer comprehensive vibration training that is highly interactive and developed specifically for the construction industry. Our safety training sessions are a mixture of practical exercises with exclusive hardware, media animations and theory.
Personal protective equipment: where health risks remain
Lastly, if there is no alternative than to expose construction workers to vibration, then it’s essential that they use relevant personal protective equipment (PPE).
A possible solution may be to provide safety gloves that help keep hands warm and support comfortable working. It’s also important that users are trained not to push too hard when using tools, to let the tool do the work. That way, they reduce the power tool vibration they are exposed to.